There are several common alternative names for screen printing: silk screen printing, and stencil printing. Screen printing is a printing technique that transfers ink through the mesh holes in the graphic areas onto the surface of hardware products by the squeezing of a squeegee, thus forming clear and firm graphics and texts.
In the field of hardware processing, screen printing technology, with its unique charm and wide range of applications, has become a crucial link in endowing metal products with individuality and functional markings.
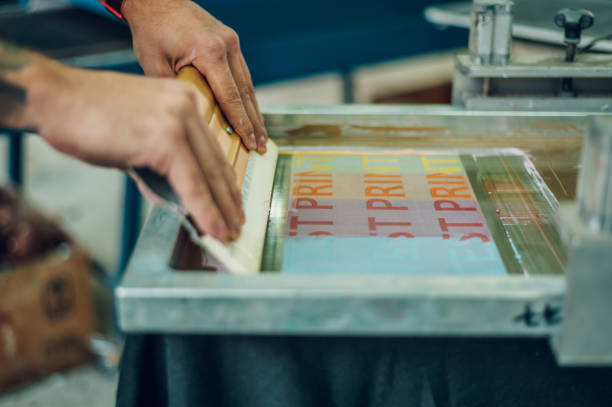
I. Principle and Process of Screen Printing Technology
1.Screen Plate Making: Firstly, the screen plate is carefully fabricated according to the designed patterns. A suitable mesh screen with a specific number of meshes is selected, and photosensitive emulsion is evenly coated on it. Subsequently, the designed graphics and texts are exposed and developed through a film, hardening the photosensitive emulsion in the graphic areas while washing away the emulsion in the non-graphic areas, forming permeable mesh holes for the ink to pass through.
2.Ink Preparation: Based on the material characteristics of the hardware products, color requirements, and subsequent usage environments, special inks are precisely mixed. For example, for hardware products used outdoors, inks with good weather resistance need to be mixed to ensure that the patterns do not fade or deform under long-term exposure to sunlight, wind, and rain.
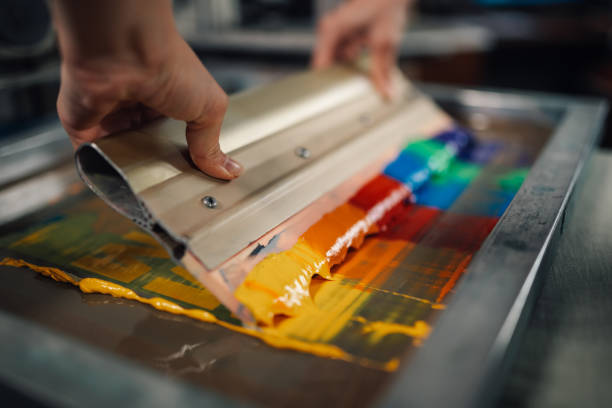
3.Printing Operation: The fabricated screen plate is tightly fixed on the printing equipment or workbench, maintaining an appropriate distance between the screen plate and the surface of the hardware product. The prepared ink is poured into one end of the screen plate, and the printer uses the squeegee to scrape the ink at a uniform force and speed. Under the pressure of the squeegee, the ink passes through the mesh holes in the graphic areas of the screen plate and is transferred onto the surface of the hardware product, thus replicating the patterns or texts consistent with those on the screen plate.
4.Drying and Curing: After printing, depending on the type of ink used and product requirements, the ink is dried and cured by natural drying, baking, or ultraviolet curing methods. This process is essential for ensuring that the ink firmly adheres to the metal surface, achieving the desired printing effect, and meeting the quality and durability standards of the product.
II. Advantages of Screen Printing in Hardware Processing
1.Exquisite Patterns with Rich Details: It can accurately present complex patterns, fine texts, and tiny icons. Both the clarity of the lines and the vividness and saturation of the colors can reach a very high level, adding unique decorative effects and artistic value to hardware products. For example, on high-end hardware accessories, screen printing can clearly display beautiful patterns and brand logos, greatly enhancing the aesthetics and recognition of the products.
2.Rich Colors and Strong Customization: A wide variety of colors can be mixed to meet the personalized customization needs of customers for the colors of hardware products. From single colors to multi-color overprinting, it can achieve colorful and layered printing effects, making hardware products more attractive and having a competitive edge in appearance.
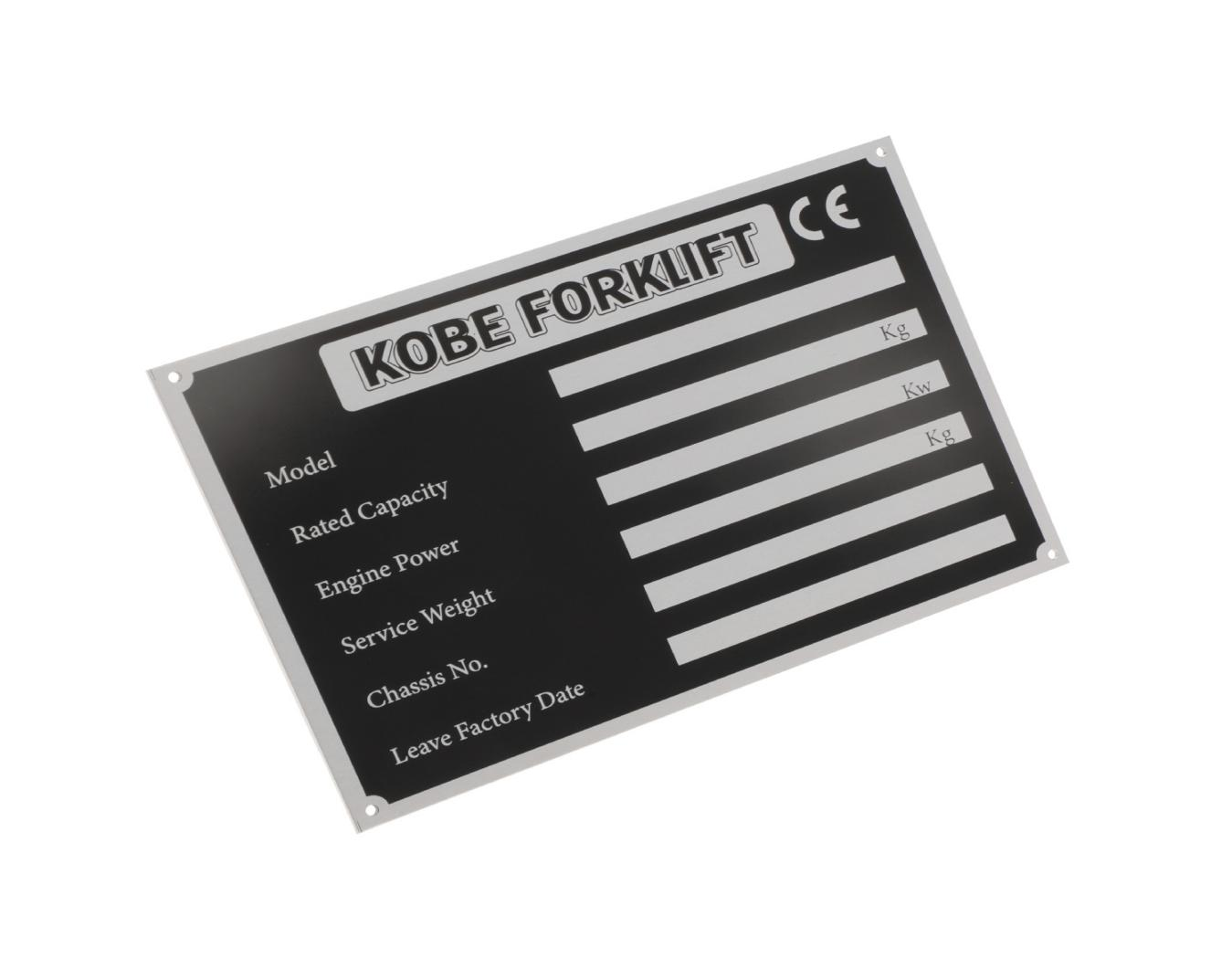
3.Good Adhesion and Excellent Durability: By selecting inks suitable for hardware materials and combining appropriate surface treatment and printing process parameters, the screen-printed patterns can firmly adhere to the metal surface and have excellent wear resistance, corrosion resistance, and weather resistance. Even under long-term use or in harsh environmental conditions, it can effectively prevent the patterns from peeling off, fading, or blurring, ensuring that the appearance quality and functional markings of the hardware products remain unchanged.
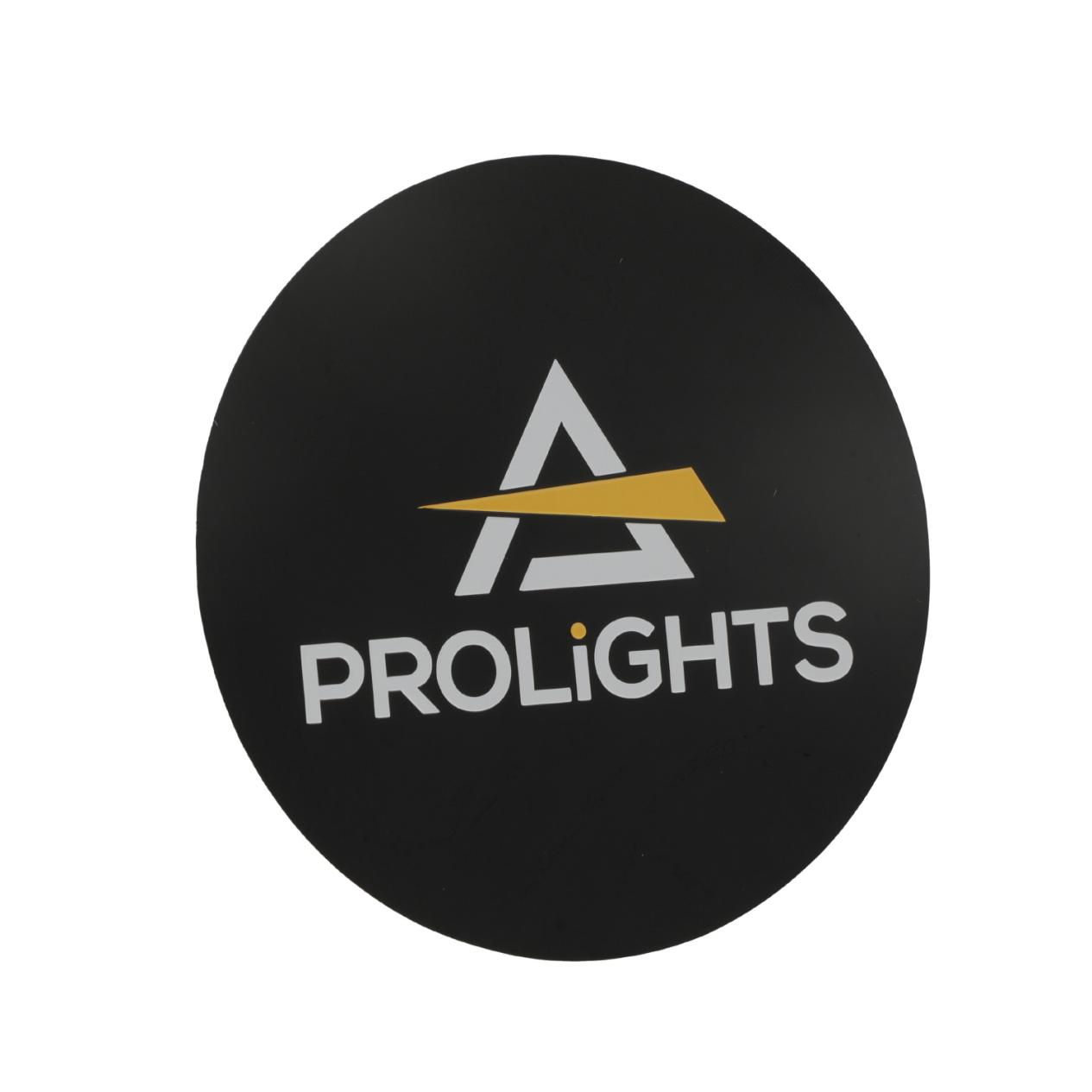
4.Wide Applicability: It is applicable to hardware products of various shapes, sizes, and materials. Whether it is flat hardware sheets, parts, or metal shells and pipes with certain curvatures or curved surfaces, screen printing operations can be carried out smoothly, providing strong technical support for the diversified product design and production in the hardware processing industry.
III. Application Examples of Screen Printing in Hardware Products
1.Electronic Product Shells: For the metal shells of mobile phones, tablets, laptops, etc., screen printing is used to print brand logos, product models, function button markings, etc. This not only improves the appearance texture and brand image of the products but also facilitates users' operation and use.
2.Hardware Accessories for Home Furnishings: On home hardware products such as door locks, handles, and hinges, screen printing can add decorative patterns, textures, or brand logos, making them blend with the overall home decoration style and highlighting personalization and high-end quality. Meanwhile, some functional markings such as the direction of opening and closing and installation instructions are also clearly presented through screen printing, improving the usability of the products.
3.Automobile Parts: The metal interior parts, wheels, engine covers, and other components of automobiles often use screen printing technology for decoration and identification. For example, on the metal decorative strips in the car interior, screen printing delicate wood grain or carbon fiber textures creates a luxurious and comfortable driving environment; on the wheels, brand logos and model parameters are printed by screen printing to enhance brand recognition and product aesthetics.
4.Industrial Equipment Markings: On the metal control panels, instrument panels, nameplates, and other parts of various industrial machinery and equipment, important information such as operation instructions, parameter indicators, and warning signs is printed by screen printing, ensuring the correct operation and safe use of the equipment, and also facilitating equipment maintenance management and brand promotion.

IV. Development Trends and Innovations of Screen Printing Technology
With the continuous progress of science and technology and the continuous upgrading of market demands, screen printing technology in hardware processing is also constantly innovating and developing. On the one hand, digital technology is gradually integrated into screen printing technology, realizing intelligent pattern design, automated printing process, and precise control, improving production efficiency and the stability of product quality.
On the other hand, the research and application of environmentally friendly inks and materials have become the mainstream trend, meeting the increasingly strict requirements of environmental protection regulations, and at the same time providing consumers with healthier and safer product choices. In addition, the combined application of screen printing with other surface treatment technologies such as electroplating, anodizing, and laser engraving is becoming more and more extensive. Through the synergy of multiple technologies, more diverse and unique surface effects of hardware products are created to meet the high-standard requirements of customers in different fields and at different levels for the appearance decoration and functional needs of metal products.
Screen printing technology, as an indispensable and important part in the field of hardware processing, endows hardware products with rich connotations and external charm with its unique advantages and wide application fields. In the future development, with the continuous innovation and improvement of technology, screen printing technology will surely shine more brightly in the hardware processing industry, helping metal products achieve greater breakthroughs and improvements in quality, aesthetics, and functions.
Welcome to quote for your projects:
Contact: hxd@szhaixinda.com
Whatsapp/phone/Wechat : +86 17779674988
Post time: Dec-12-2024